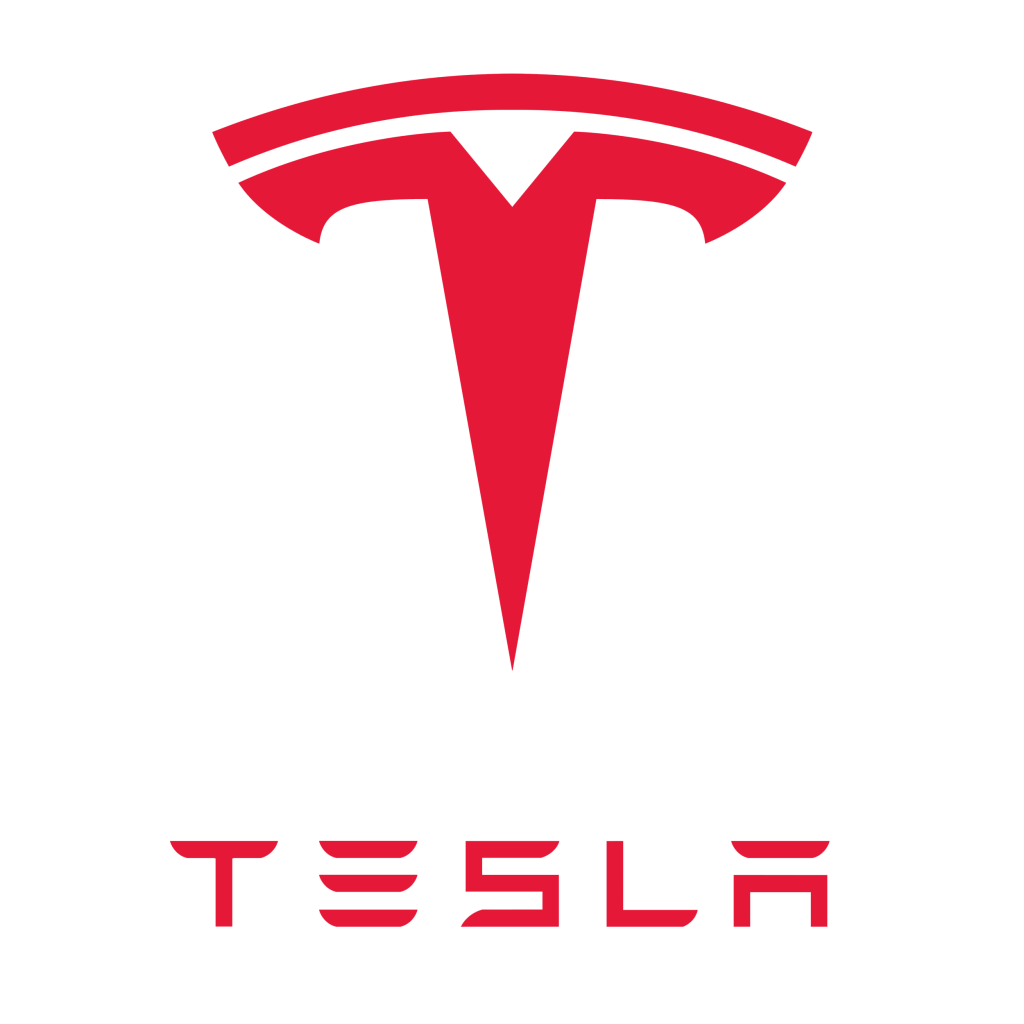
Tesla – Sr. Product Support Engineer
01/2021 – 09/2022
Remote – Whistler, BC
- Engineering lead for closures electromechanical components across all vehicle models.
- Coded vehicle software to show alerts and warnings on vehicle UI. Released to customer vehicles via over-the-air software updates.
- Performed data analysis and statistical modelling to estimate failure rates for recall campaigns. Utilized Spark and Presto for data processing.
- Led proactive design efforts to optimize design for serviceability on cybertruck and semi truck platforms.
My work in the press:
- Tesla releases app update with solution for frozen door handles
- Root cause analysis for windows freezing issue. Reviewed suspected hardware and software logs on customer vehicles. Recommended solutions to executive teams. Oversaw and validated implementation.
- How Tesla pivoted to avoid the global chip shortage that could last years
- Key stakeholder in validating new chip supplier for Model S door handles. Tested and validated new parts to ensure equal functionality.
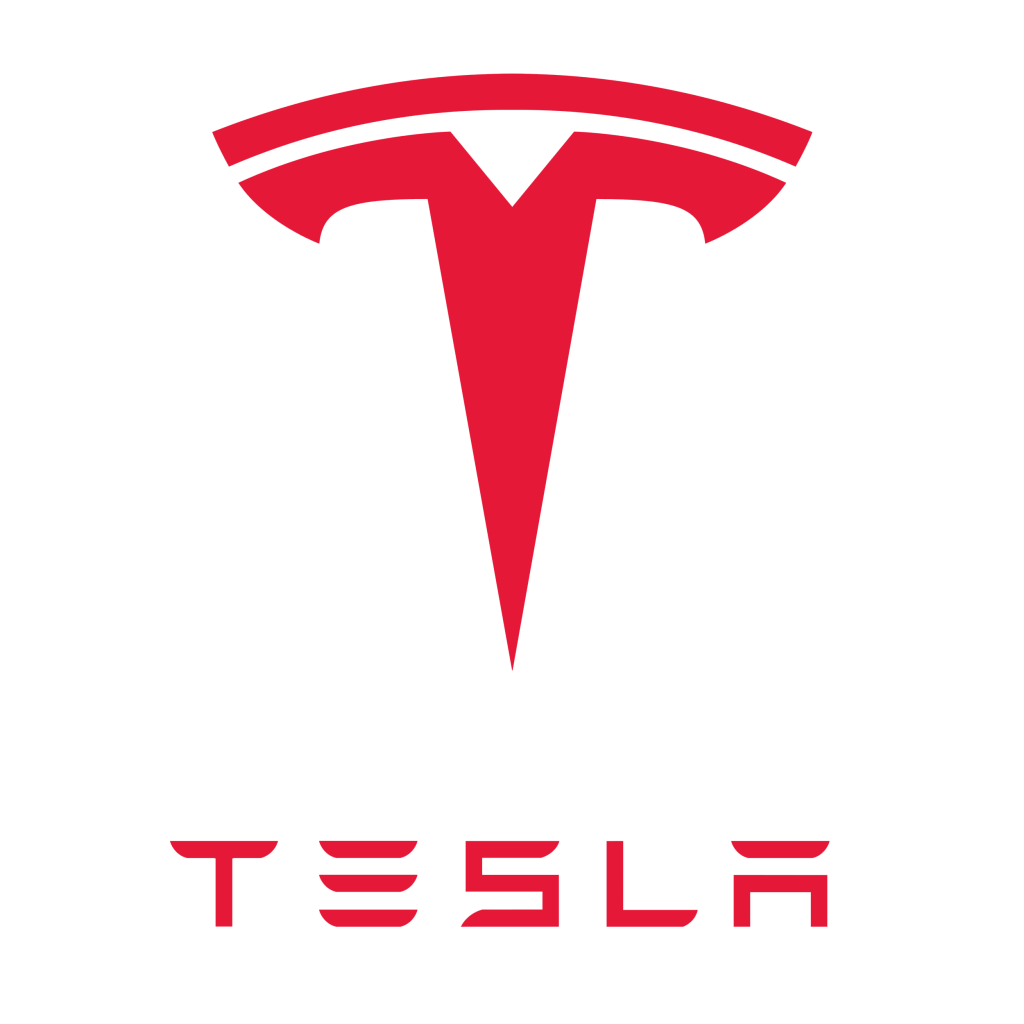
Tesla – Sr. Quality Engineer
11/2016 – 01/2021
Fremont, California
- Subject matter expert for automated testing of vehicle systems within Fremont factory (low/high voltage, HVAC, cameras, sensors etc). Utilized python and C++ programming.
- Spearheaded root cause analysis on several major quality issues, completed reporting to executives and containment strategies.
- Set priority for quality issues to factory executive leadership to decrease ambiguity. Developed real-time data pipelines with data science team to ingest manufacturing data and determine highest priority issues.
- Led and pushed forward development of automated vision inspection system in Fremont factory. Used to record and alert non-conformances in manufacturing stations.
- Key stakeholder in development of machine learning system to simplify complex repair issues on completed vehicles.
- Led torque control system within Fremont factory, supervised torque audit technicians, equipment adjustments/validation, ultrasonic studies for clamp load validation.
- Maintained and grew relationships with part suppliers – commissioning new processes, root cause analysis, cost recovery, quality assurance.
- Designed and fabricated equipment for use in production. Integrated with existing systems and processes.
My work in the press:
- Tesla is pushing to achieve Model 3 production of 7,000 units per week within 2 weeks
- “Voice of customer” in reviewing automated quality testing under microscope to remove redundancies. Developed new quality testing strategies with less impact to production time. Performed validation to ensure no impact to quality.
- Elon Musk reveals Tesla Model Y production ramp-up problem in leaked email
- Solved several significant issues in GA4 tent facility. Ex. Wifi signal dropping causing delays in production. Reviewed logs from vehicles, wifi extenders and IT infrastructure to optimize vehicle communication. Worked with IT team to develop monitoring tools for immediate response to issues.
- Tesla is looking to implement new automated camera system for quality inspection at Fremont factory
- Lead engineer on pushing and validating first phase of camera inspection. Performed trials on several technologies including an in-house developed option. Integrated equipment with manufacturing line. Selected locations for most effective inspection. Hired and trained personnel to assist with project development.
- Tesla has some major Model Y quality issues
- Manually reviewed customer concerns to prioritize work in production. Used data to launch new manual and automated testing in production to eliminate issues.
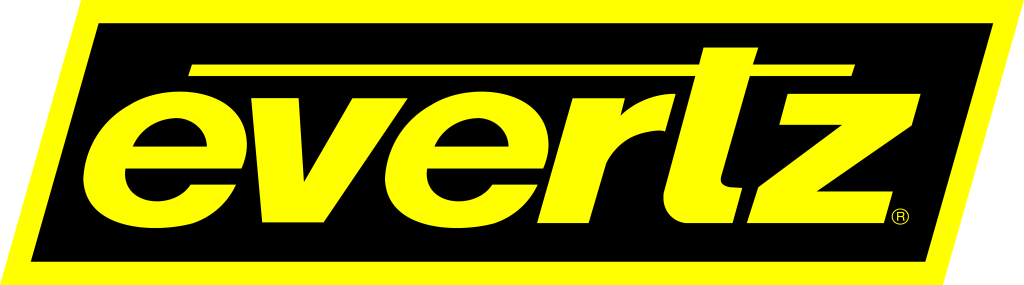
Evertz – Field Engineer
12/2014 – 06/2016
Burlington, Ontario
- Lead engineer on remote product deployments:
- Commissioning slow motion replay systems for MLB (Major league baseball) and NBA (National basketball association)
- Launch and commissioning of new AV product line for Morgan Stanley and Bridgewater banks.
- On-site work included diagnosing electrical and software issues, providing direction to customers and collaborating with engineering teams during development process.
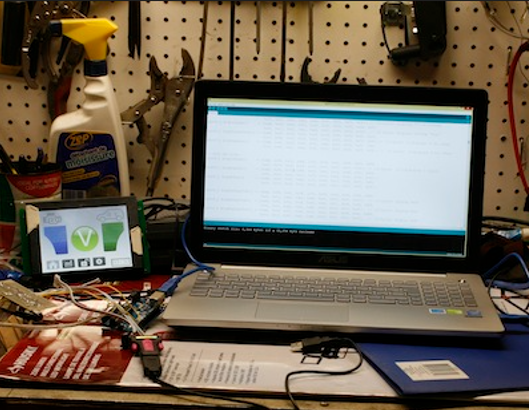
Waste cooking oil vehicle fuel system – University project
09/2013 – 05/2014
Hamilton, Ontario
- A team of myself and 4 other students researched, designed and developed low-cost system to re-use waste cooking from restaurants as fuel in my 1992 VW Golf.
- The system included a touch display that provided real time feedback of system performance (fuel levels, temperature readings, trip efficiency, etc.)
- An analog fail-safe device was also developed in case the vehicle was shut down while running waste cooking oil. The fail-safe device would purge the fuel system with diesel after the key was removed from the ignition.